REPOUSSÉ
Hand-hammering decorative relief onto sheet metal
- Originated around 800BC between Asia and Europe, and in Chinese Han Dynasty (206BC-AD220).
- Uses a hammer, and various shaping tools - achieved by working on both sides of the sheet metal.
- Hand-chasing metal begins with mallet blows at the center of the sheet metal, continuing out to the edges, never striking the same spot twice.
- The metal is then heated and worked until properly formed.
CLOISONNÉ
Enameling on metal technique
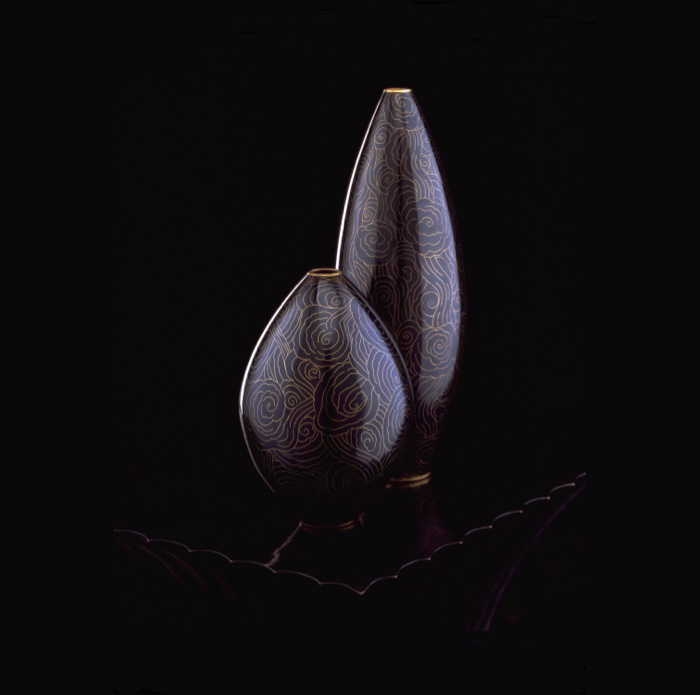
- From the Byzantine Empire and reached China around the 12-13th century.
- Cloisonné requires these steps:
- Form the metal base (= Repousse Copper).
- Form wires by hand to outline the design.
- Solder the wires in place to form ‘cloisons’ or cells.
- Mix the colors that contain heat proof metal oxides.
- Fill the cells/cloisons with enamels. Fire piece in kiln. Colors are fired according to their burning rate. Shrinkage occurs, Refill and fire until the cell is filled.
- Hand-sanding with carborundum to smooth.
- Polishing.
- Gold plating the wire cells.
- Traditional cloisonné limited design innovation and experimentation.
- In the 1980's, Robert Kuo began his repertoire with cloisonné and introduced flowing designs without compromising technical quality.
LACQUER
Translucent sap from trees (rhus verniciflua) and the technique
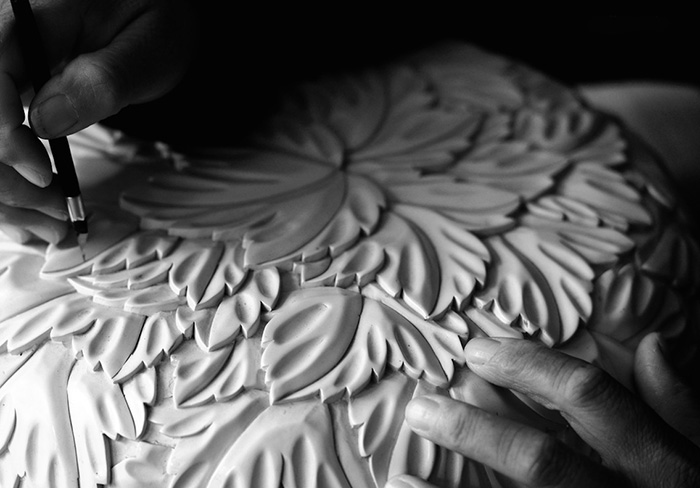
- Dates back to the Shang Dynasty, c. 1600-1100 B.C.
- Lacquer pieces are made with at least 60 coats of organic lacquer, or 1 to 2.5 mm thickness, applied over a base (wood or metal).
- After sap is tapped from trees, lacquer is boiled and strained to rid of impurities and prepare as a coating.
- The lacquer technique applies multiple thin layers, waiting 24 hours between each layer so that the lacquer can cure and dry.
PEKING GLASS
Chinese Glassmaking
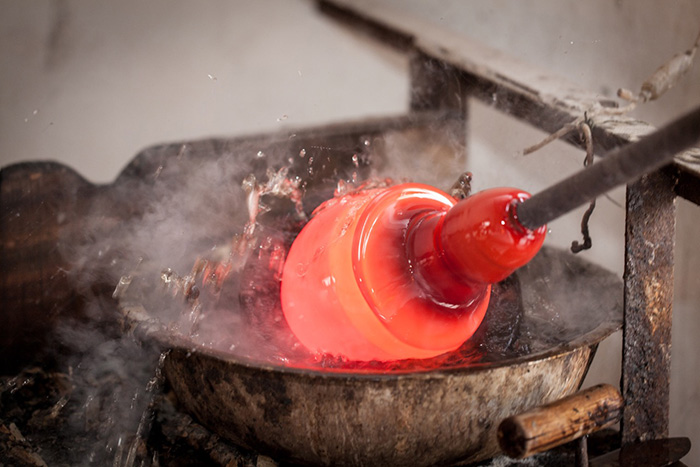
- The glassblower begins with a piece of molten glass that is blown and formed into an initial shape. While still molten, another layer of molten glass is added to the piece and then blown some more. As many as six layers of glass may be added then blown again into its final form.
- The glass vessel must cool very slowly over several days. If allowed to cool too quickly, the thick glass will craze and crack.
- Finishing uses the same methods and techniques used in jade carving. Carving and grinding the glass often cuts into the inner layers of glass to add surface complexity and depth to the piece.
- Robert Kuo has experimented with color combinations, with combinations of opaque and clear glass, and with carving techniques to achieve a depth of color, surface interest, and richness not found in earlier pieces. Robert Kuo expands the tradition by designing pieces that compliment the classic shapes while presenting a clearly contemporary attitude.